AnywhereAmps - Alpha 1.1
Mobiler Instrumenten-Verstärker/Cabinet-Kombi-Prototyp Version 1.1, entwickelt aus AnywhereAmps Alpha.
Projekt-Statistiken
- Schwierigkeit: mittel 3/5
- Kosten: ~200€ plus Batteriesystem
- Zeitaufwand: 3h
Aktualisierungen gegenüber Alpha 1.0:
- Hinzufügen einer Stromüberwachungsschaltung, um sowohl den Verstärker als auch das Akkupack vor abnormalen Spannungen / Strömen zu schützen
- Integrierter Ein/Aus-Schalter im Potentiometer
- Geringere Komplexität durch Verwendung eines hocheffizienten Breitbandlautsprechers anstelle eines 2-Wege-Systems mit 3 Lautsprechern
- Hinzufügen eines hocheffizienten Abwärtswandlers zur Erzeugung einer 9-V-Effektspannungsschiene
- Geringere Bauzeit durch Verwendung einer kundenspezifischen Leiterplatte mit Vorverstärker, Abwärtswandler und “Power Supervisor”
- Reduzierte Bauzeit, da Großteil der Holzarbeiten an eine Portalfräse (CNC1) ausgelagert werden konnte
- Einschaltknackgeräusche eliminiert durch Hinzufügen eines RC-Filters zum Standby-Eingang der Endstufe
Bauvarianten
Um den Klang meines Prototyps weiter zu verfeinern, habe ich dieses Mal verschiedene Varianten gebaut. Ich habe die Chassis ausgetauscht und den Klang bewertet:
- Alpha 1.0: 30W gebrückter Verstärker, 4” Bass und 2x Piezo-Hochtöner: HiFi-ähnlicher Sound mit druckvollen Bässen und klaren Höhen, limitiert in der maximalen Lautstärke
- Alpha 1.1 v1: 30W gebrückter Verstärker, 4” PA-Treiber, gute Lautstärke und hohe Präsenz, aber unterrepräsentierte Bässe und Höhen
- Alpha 1.1 v2: 30W gebrückter Verstärker, 4” PA-Treiber und Passivmembran, satte Bässe aber etwas dumpf in den Höhen
Meine eigene Platine für Vorverstärker und Zusatzfunktionen
Die AnywhereAmps 1.1 PCB bietet neben dem reinen Vorverstärker plus Tiefpass und Hochpass für Bi-Amping noch einige Zusatzfunktionen. Die Details sind in den folgenden Abschnitten beschrieben.
Power Supervisor
Ich habe eine Power Supervisor-Schaltung hinzugefügt, um zu verhindern, dass die Batterie komplett leer gezogen wird. Außerdem wollte ich die Risiken durch Kurzschlüsse und andere Fehlerzustände, die die Batterie beschädigen könnten, verringern. Die Integration dieser Technologie funktionierte auf Anhieb (was ich nicht erwartet hatte). Der einzige Nachteil ist, dass der Verstärker bei einer Entladung der Batterie auf z. B. 10 % manchmal neu startet, wenn die Versorgungsspannung unter die Auslösespannung des Überwachungsgeräts fällt. Da die Batteriespannung wieder ansteigt, wenn die Last abfällt, schaltet er sich eine Sekunde später wieder ein.
Dies ist eindeutig ein unerwünschtes Verhalten und muss in einem weiteren, verbesserten Prototyp behandelt werden. Ein weiterer Punkt, der diesen Folgeprototypen notwendig macht, ist die Tatsache, dass ich in meinen zukünftigen Entwürfen keine Batterien des Werkzeugherstellers verwenden darf wie hier diskutiert.
9V Abwärtswandler
Zur Erzeugung von zusätzlichen 9V für Geräte wie Effekte, Looper usw. verwende ich einen Schaltregler. Ich wollte das Rauschen reduzieren, indem ich einen “leisen” Schaltregler wählte. Der von mir gewählte Regler wurde für Anwendungen im Automobilbereich entwickelt und hat die Induktivitäten in seinem Gehäuse integriert. Von Nachteil ist, dass der Baustein kaum von Hand gelötet werden kann. Außerdem ist er sehr teuer.
Der Wandler schaltet sich ein, wenn ein Gerät in die entsprechende Buchse eingesteckt wird, so dass es keinen Standby-Strom gibt. Er arbeitet leise (aber nicht ganz rauschfrei) und bietet mehr als genug Leistung für die Anwendungen, die ich bisher habe - ein Looper, ein Kompressor und ein Tuner können problemlos parallel betrieben werden.
Holzbearbeitung
Ich habe ein Portalfräsmaschinen-Set gekauft, um die Holzbearbeitung für AnywhereAmps zu delegieren. Ich wollte weniger Zeit für Sägen und Schleifen aufwenden und die Verarbeitungsqualität sowie die Wiederverwendbarkeit verbessern. Aber um die manuelle Holzbearbeitung durch eine mehr oder weniger automatisierte Bearbeitung zu ersetzen, musste ich zunächst meine Pläne in die digitale Welt übertragen.
Computer Aided Design
Ich wählte FreeCAD als Konstruktionswerkzeug, um Zeichnungen zu erstellen. Die Arbeit damit habe ich in einigen posts dokumentiert und meinen Arbeitsablauf z.B. hier weiter verbessert. Meine erste Skizze zur Herstellung sah so aus.
Mit der Aufteilung der Holzplatte war ich noch nicht ganz zufrieden. Ich fand die Beine zu lang und habe noch einige Stunden in die Verfeinerung des Entwurfs investiert, um weniger Platz zu benötigen, da die Kapazität meiner Portalfräse begrenzt ist.
Computer Aided Manufacturing
Als ich fertig war, exportierte ich die Skizzen als *.dxf-Dateien (Drawing Interchange File Format (DXF), 1982 von AutoDesk eingeführt. Es wurde schließlich zum Industriestandard für den Austausch von 2D-Zeichnungen) und öffnete sie in meinem CAM-Werkzeug, um Werkzeugwege zu definieren, den XY-Nullpunkt und die Z-Tiefe pro Durchgang festzulegen.
G-Code
Am Ende erhält man G-Code-Dateien, die so nachbearbeitet waren, dass sie zur Maschine passten, mit einer geschätzten Bearbeitungszeit von 32 Minuten pro Exemplar. Ich verwendete nur drei Werkzeuge: einen 6-mm-Fräser für die Ausschnitte, einen 2-mm-Fräser für kleinere Löcher und Strukturen und ein Gravierwerkzeug für Fasen und das Logo. Ich teilte die Arbeit in drei Aufträge auf:
job00_clamping
, um Löcher und Senkungen zu schneiden, damit das Werkstück am Maschinenbett befestigt werden kannjob01_nesting
, um alle Ausschnitte zu fertigen und Gravuren auf dem Verstärkerträger zu machen, aber Anbindungen stehen zu lassen, damit sich die Teile nicht losreißenjob02_finishing
, der das Logo auf die (bereits gefärbte) Oberseite graviert und Fasen hinzufügt, wo es nötig ist
Für die Endbearbeitung musste ich die CAD- und CAM-Dateien aktualisieren, damit sie eine gespiegelte (und um -90° gedrehte) Ansicht des Werkstücks liefern. Dies ermöglicht das zweiseitige Fräsen mit demselben XY-Nullpunkt und den exakt gleichen Seiten, die den Anschlag berühren, um minimale Toleranzen zu erzielen.
Nacharbeit
Ich musste noch ein wenig Handarbeit leisten, z. B. Gewindebohrungen abschleifen, Wachs für eine bessere Oberfläche auftragen, und einige Löcher für Streben und Ständer schneiden, die meine CNC nicht fertigen konnte.
Mit der CNC habe ich Adapter für meine Handoberfräse hergestellt, damit sie über die gebogene Oberfläche des Zylinders gleiten kann. Auf diese Weise konnten die Löcher, die ich zuvor für die Lautsprecher geschnitten hatte, richtig abgeschrägt werden.
Außerdem ließ ich von der CNC eine Halterung für das Gehäuse im 3D-Modus anfertigen (mit *.STL-Dateien). Auf diese Weise wird der Kessel an seinem Platz gehalten, wenn ich mit meiner Handbohrmaschine Löcher für die Lautsprecher bohre. Übrigens: 3D-Fräsungen brauchen viel Zeit, da die Nachbearbeitung in kleinen Schritten erfolgt, um eine glatte Oberfläche zu erhalten.
Das Bohren von Löchern mit einem Durchmesser von mehr als 100mm
von Hand lässt keine gute Oberflächenqualität auf der Innenseite des Gehäuses zu und die Handhabung des riesigen Bohrers ist immer noch eine Qual. Leider ist meine CNC nicht in der Lage, diese Aufgabe für mich zu übernehmen, daher wird das wohl weiter ein manueller Prozess bleiben.
Eindrücke

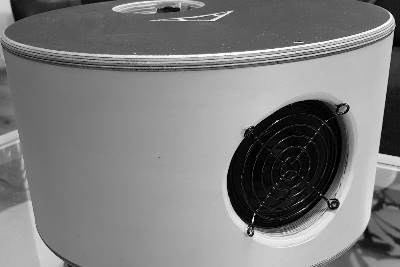
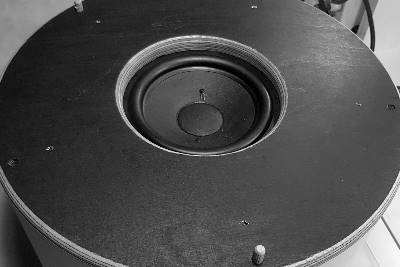
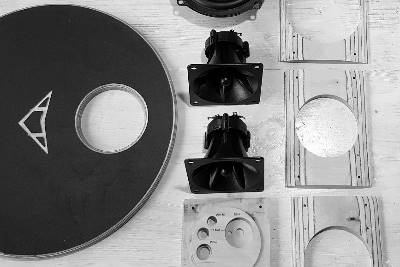
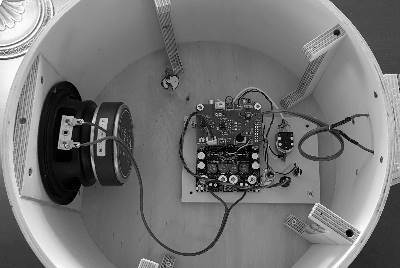
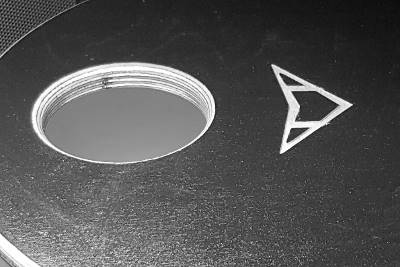
-
Computerized Numerical Control ↩